THERMOGRAPHY OF SOLAR PANELS
Fault localisation and characterisation. Analysis of energy losses and risks for the installation.
Photovoltaic park thermography
Inspect PV plants and target energy losses
Since 2012, we have inspected several hundred solar installations.
Feedback and our regular exchanges with our customers ensure that you have a good inventory of faults and the condition of your plant. After each thermal inspection, a meeting is scheduled to ensure proper use and understanding of the renderings.

The defects of photovoltaic power plants
Classification of thermal anomalies
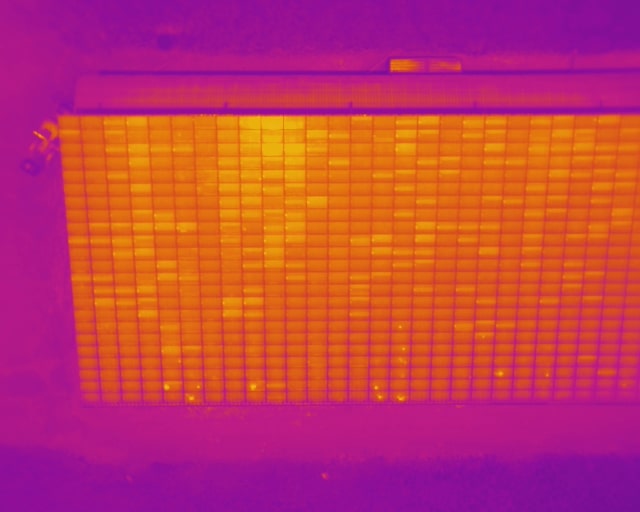
HIGH YIELD LOSS
Each type of fault generates an energy loss ranging from a few % of production to complete faulting of several modules.
Depending on the plants, these faults can represent a shortfall of up to 45% of production in the most critical cases.
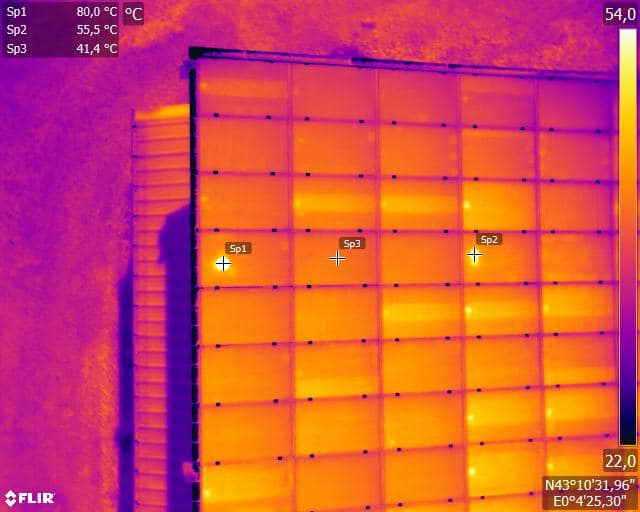
DESTRUCTIVE RISK
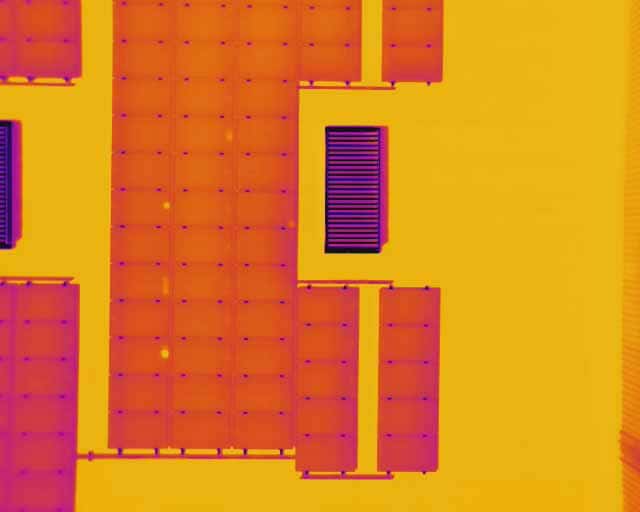
MINOR DEFECTS
Thermal faults that do not involve any destructive risk or significant loss of yield are classified as minor faults.
These faults are located on the photovoltaic power plant and categorised by type. We also sort them according to the temperature difference with “healthy” solar panels.
Orthoplan | Geolocalisation | Wedging on plan
An interactive thermal inspection report
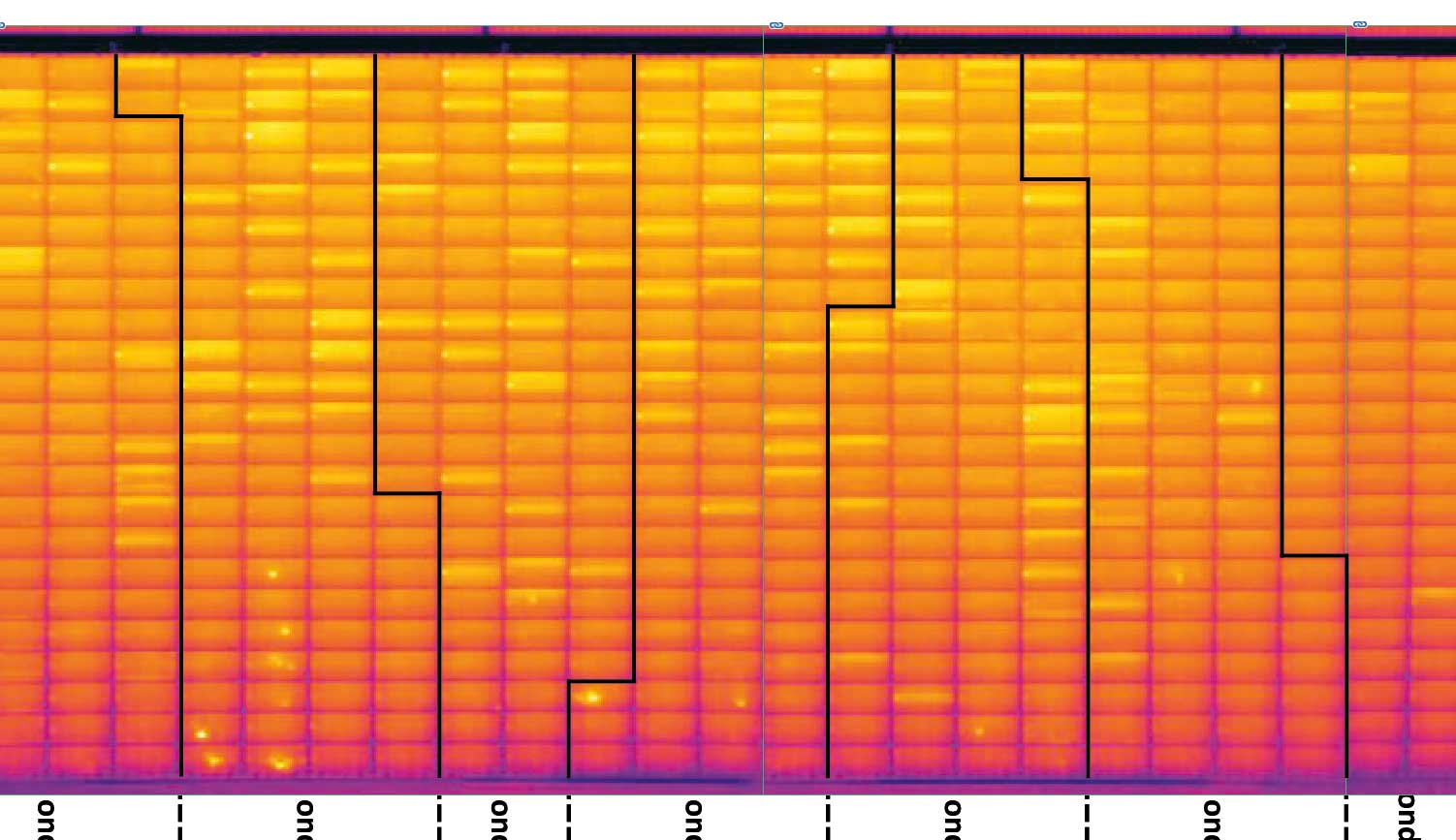
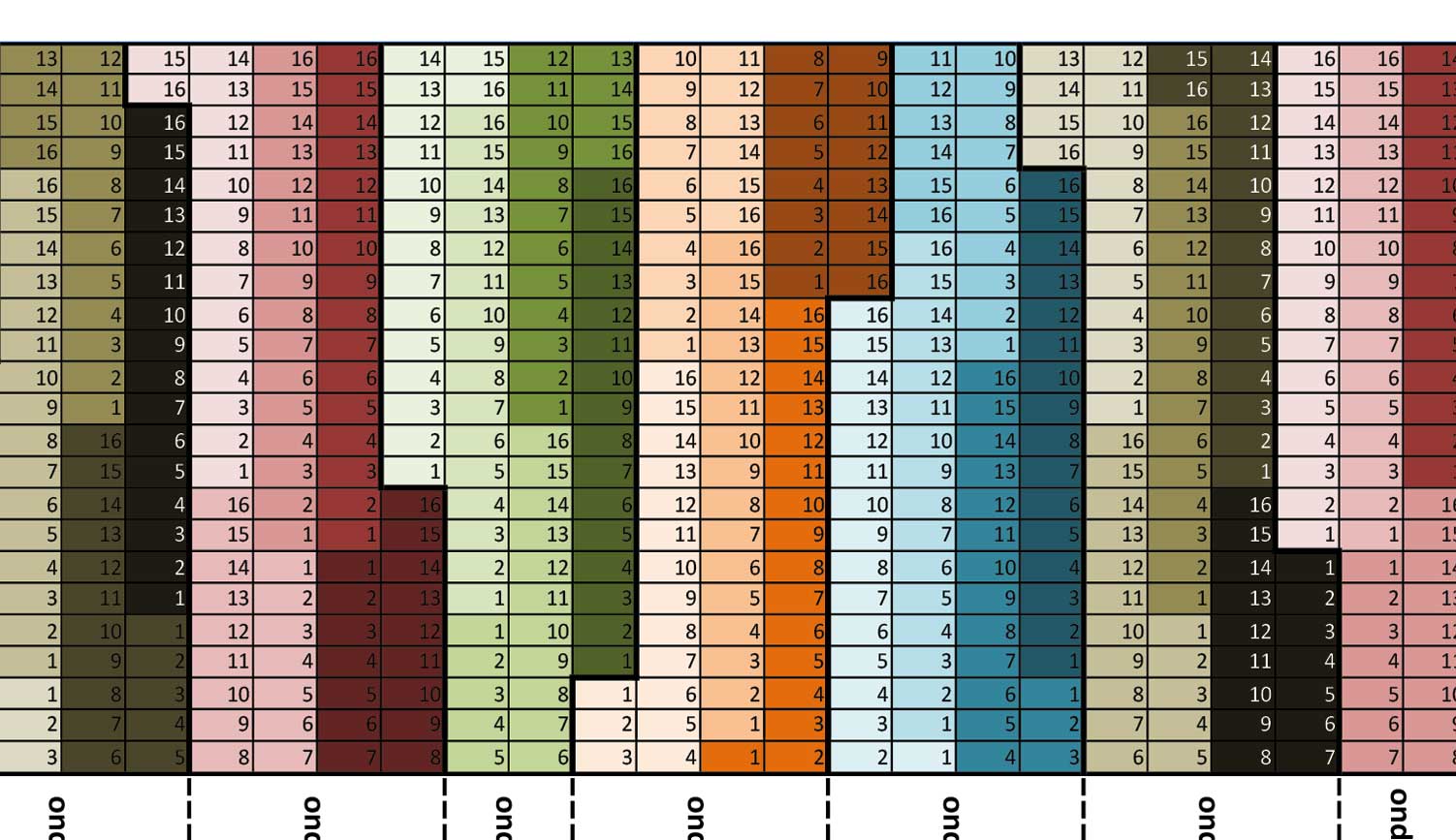
An RGB stitching is also made to get an overview of the solar installation in the visible range.
To do this, we make many thermal images on the installation that we assemble in our treatment process.
This allows us to keep the thermal information of the thermograms which will be used to classify the defects with precise measurements.
This assembly is then superimposed on the plan of your solar power plant with a layer system.
This allows you to quickly switch between layers to identify the number of defective panels.
- 5Thermal assembly
- 5Overlay on plant plan
- 5Interactive report
During the thermal inspection of the plant, we also produce “classic” so-called RGB images. These images allow us to better identify the nature of the defects when the thermal image is not enough (crack, presence of dirt)

The conditions for a good thermal inspection
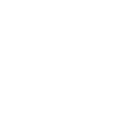
Sunshine
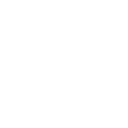
Panel cleanliness
A clean plant reduces the number of false positives.
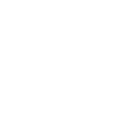
Period of the year
We advise to inspect in the period between April and October.
Abnormalities
The different types of thermal faults
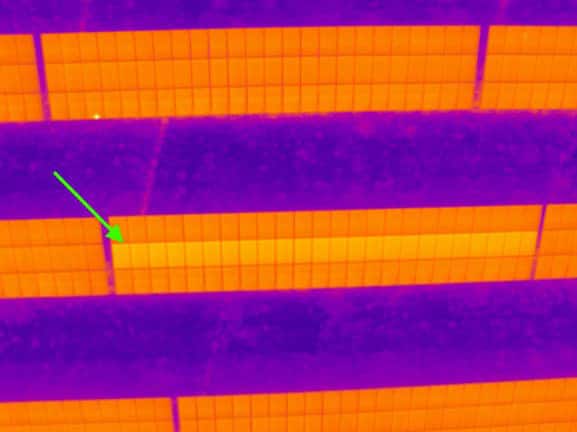
Full thong
Photovoltaic module fault : One module is hotter than the others. (a full line)
Error and possible cause : Panel malfunction. The module is disconnected.
Consequence : Zero production.
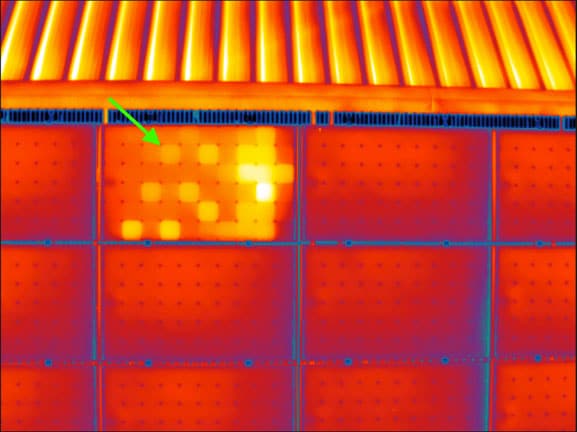
PID
PID (Potential Induced Degradation) : Constellations of cells hotter than the others.
Error and possible cause : Short circuit, faulty bypass diodes, broken panel.
Consequence: Performance loss
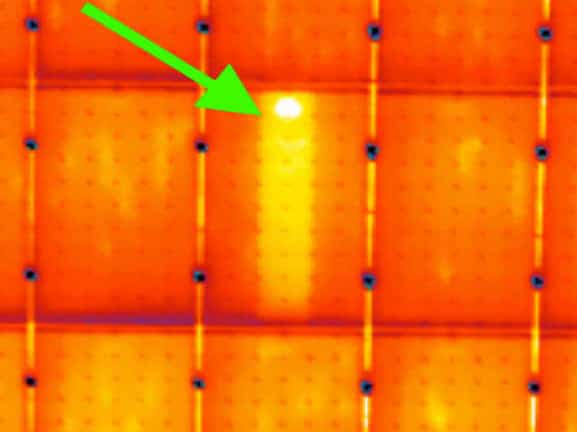
Bypass diode
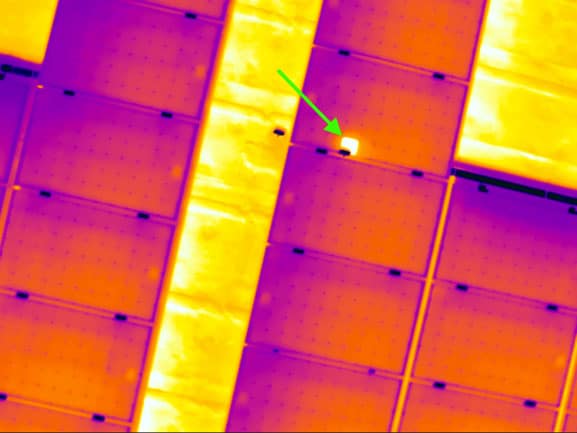
Hot spot
Hot spot fault : A cell is much hotter than the others making up the photovoltaic panel.
Error and possible cause : The cell is defective.
Consequence: Performance loss. A visual and more thorough inspection is required.
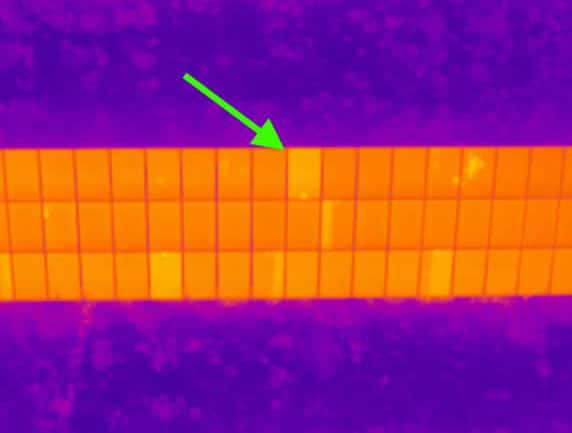
Defective module
Default of a string of modules : A line of panels is warmer than the others.
Error and possible cause : A defective panel can cause the entire string to malfunction.
Consequence: Performance loss over the entire series.
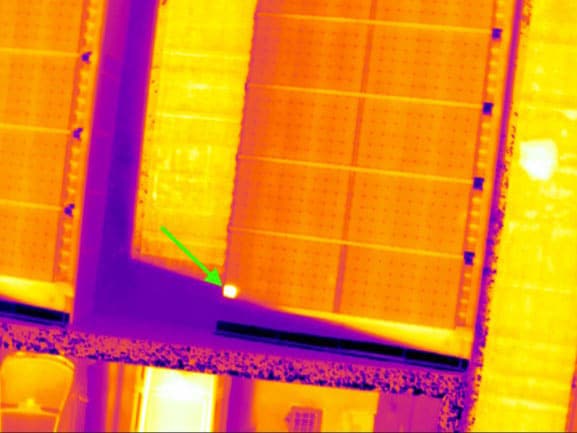
Cell shading
Shaded cell : A cell is much hotter than the others.
Error and possible cause : The photovoltaic cell is shaded. Vegetation, a building, dirt, etc. conceal it.
Consequence: Performance loss of the cell as well as the entire solar panel.
Our expertise in aerial thermography also extends to other sectors of activity :
- 8, rue de la Madeleine - 69007 LYON
- 04 37 28 67 25
- contact@studiofly.fr
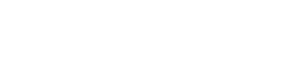
Discover our entity dedicated to audiovisual production
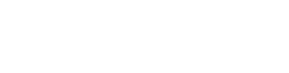